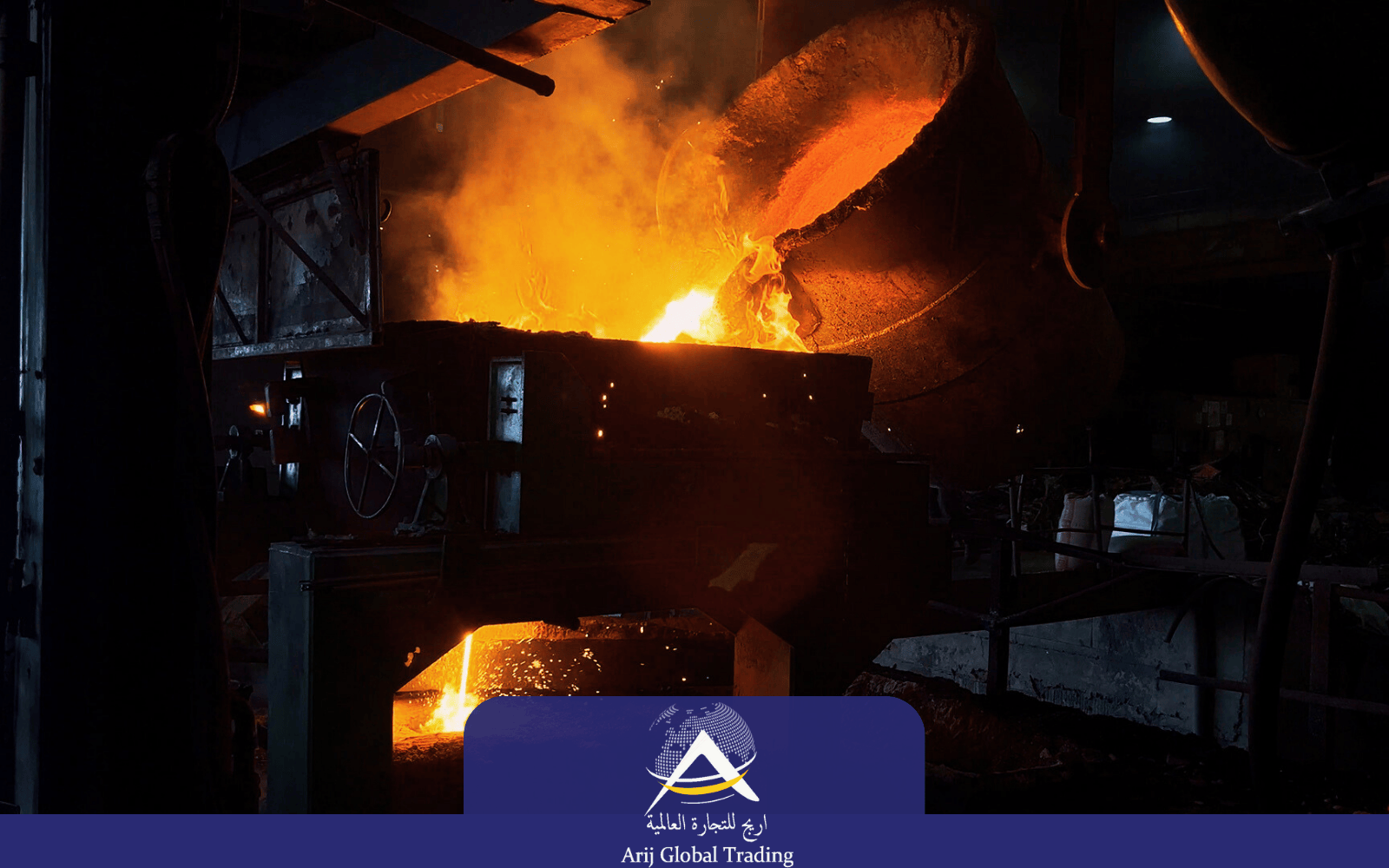
Steelmaking Methods
One of the most important industrial processes is steel manufacturing. It has followed civilization’s technological development because of its characteristics of high strength and ductility. In fact, three different ways of steel production are:
- The Blast Furnace (BF)
- The Direct Reduction (DR)
- The Electric Arc Furnace (EAF)
The Blast Furnace (BF) plants were built for the production of large amounts of steel. The melting metallurgical process begins with the reduction of iron ore. In the BF, cast iron is produced, and after that, oxygen is blown into steel by the converter.
Direct Reduced Iron (DRI) is usually used in its briquette form (Hot Briquetted Iron (HBI)) for easier transportation, and it can be charged in the blast furnace (BF), inside the converters (BOF) and in the Electric Arc Furnace (EAF).
The cycle of EAF is based on the melting of metal scrap. The HBI manufacturing process involves the usage of a reformer with the conversion of natural gas to hydrogen (H) and CO (the reducing gas) in a vertical furnace. This furnace creates the reduction reactor and a heat recovery unit. Energy-wise, the production process is cheaper if compared to cast iron production since it is not essential to make the iron ores reach the melting temperature, contrary to the blast furnace (BF). In addition, establishment costs are considerably less than the full cycle of steel manufacturing.
Sustainable steelmaking goals
The final goal of modern society is to reduce the environmental effects, especially for the iron and steelmaking industries. According to one of the researches[1], the sustainable steel-making goals are:
- preservation of natural resources,
- reduction of greenhouse gas emanation,
- reduction of volatile emanation,
- reduction of landfill waste,
- reduction of dangerous waste.
BF/BOF vs EAF
Comparing the properties of iron and steelmaking technologies:
- BF/BOF has consumption of equipment and emissions 2-4 times higher, and this requires more energy & water consumption. Moreover, it needs higher energy for production due to the coke-making and sintering processes.
- EAF somehow has larger emissions of greenhouse gas of produced metal compared to DRI, mostly due to the use of electricity; at the same time, in the DRI process, only natural gas is applied to reduce the iron ore. The emission of SO2 CO is not meaningful in DRI technology.
The use of the DRI as a substitute for cast iron to increase the cold charge in BOF is innovative.
HBI Advantages
The HB I’s advantages are:
- high electrical and thermal conductivity;
- high bulk density, which saves space;
- minimum reactivity with salt & freshwater.
- chemical properties are well-known & verified by the producers;
- the lowest value of harmful elements, such as Cr, Sn, Cu, Ni, Mo, V, and Pb;
Use of DRI and HBI in a blast furnace (BF)
DRI and HBI are used in BF to produce pig iron. Right before the melting time, the BF is involved in the presence of DRI, so the charging of DRI and HBI targets evading the reduction processes required to reduce only a fraction of the charged raw material.
Use Of DRI and HBI In Basic Oxygen Furnace (BOF)
The BOF steelmaking process consists of 3 main steps:
- converter charge;
- blowing of the oxygen;
- using the ladle.
A bright further reduction in coke consumption and an increase in blast furnace productivity can be achieved by the introduction of DRI and HBI enriched by carbon.
Use Of DRI and HBI In Electric Arc Furnace (EAF)
The physical composition of DRI and HBI and their perfect allocation inside the EAF buckets influence the quality and the metallurgical yield.
DRI and HBI melt very fast because of the great conductive heat transfer. Thus, it must be charged to the second bucket. A suitable charging of DRI and HBI will help stabilize the arc and protect the furnace lining.
When DRI is charged, the key factors affecting the consumption of electricity are:
- Quality of DRI AND HBI, including contents of Fe M (metallic iron), C (carbon), SiO2/Al2O3 (gangue), S (Sulfur), and P (Phosphorus);
- The temperature of DRI AND HBI;
Conclusions
DRI and HBI usage in a blast furnace (BF) allows the reduction in charged coke, the emission of CO2 and the concentration of Sulphur in the tapped cast iron;
in the BOF and in the EAF, a properly carburized metal bath, such as pig iron, lets the recovery of the FeO in the DRI and HBI on;
in the EAF way, DRI and HBI don’t have to be charged by the first bucket since this kind of raw material needs to be added to a molten bath enriched by carbon
New steelmaking processes: drivers, requirements and potential impact. Fruehan. s.l. : Ironmaking Steelmaking,2005, Vol. 32.
Related products: