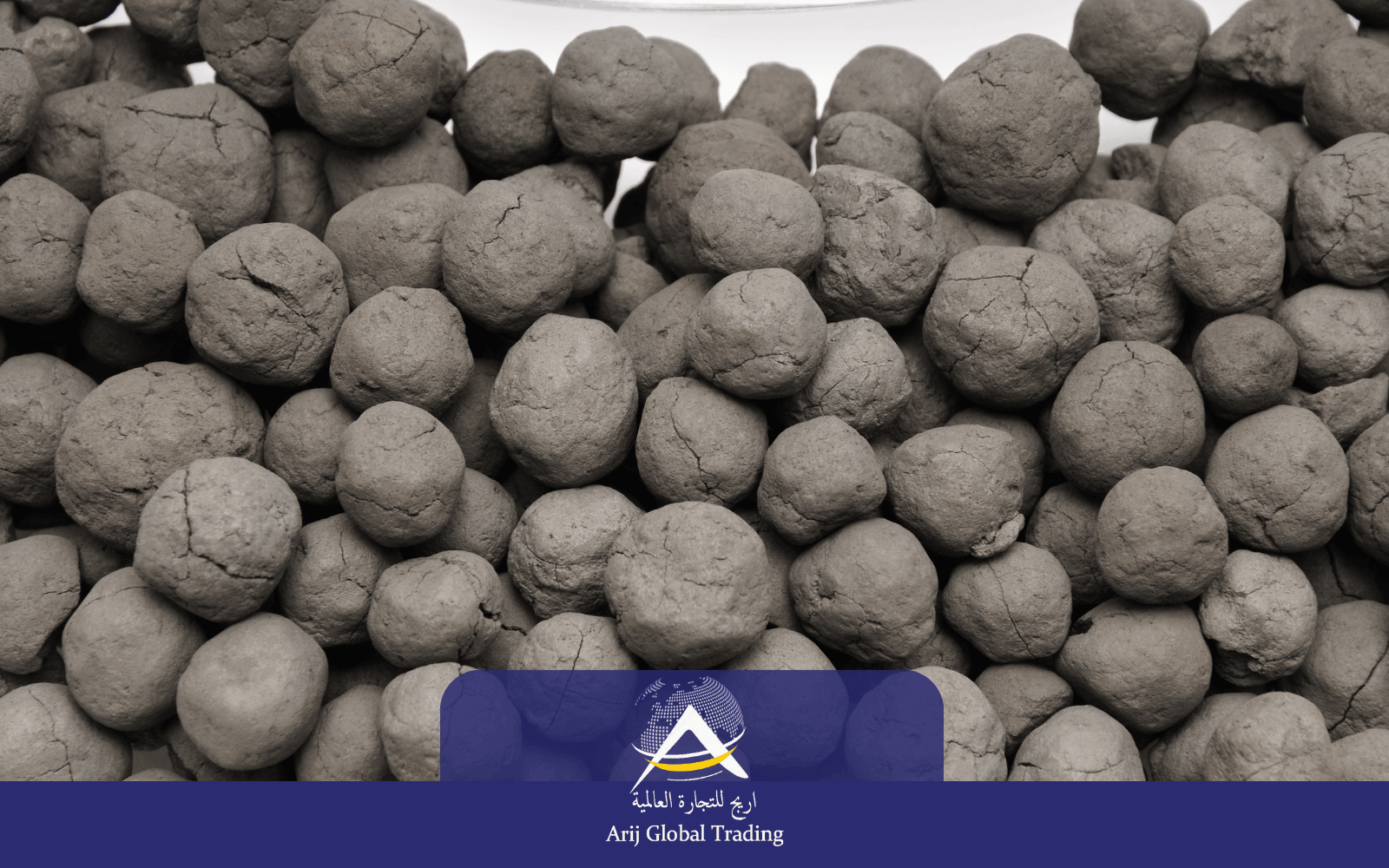
The uses of DRI in modern steel production are more relevant than ever as the industry shifts towards more efficient and sustainable processes.
In today’s evolving steel industry, Direct Reduced Iron (DRI) has become an indispensable resource for producers aiming to optimize quality, reduce emissions, and manage costs more effectively. Whether you’re running a mini-mill or a large-scale integrated facility, the strategic use of DRI can deliver measurable operational benefits. As a seasoned DRI supplier and DRI exporter, we understand the logistical and technical challenges steel producers face. Partnering with the right DRI supplier ensures not only consistent product quality but also timely delivery and expert consultation throughout your procurement cycle., we’ve had the opportunity to support a wide variety of steel manufacturers, and this article brings together that real-world experience to help you understand the top uses of DRI in modern steelmaking—an increasingly vital component in high-efficiency steel production strategies.
What Is DRI and Why Is It Gaining Global Attention?
Direct Reduced Iron (DRI) is produced by reducing iron ore in its solid state—without melting it—typically using a gas or coal-based reduction process. The result is a highly pure iron product that serves as a clean, consistent alternative (or supplement) to scrap metal.
The growth in demand for DRI is driven by multiple factors:
- Volatility in DRI price is still more manageable than scrap fluctuations.
- Increasing emphasis on sustainable production.
- The shift toward Electric Arc Furnace (EAF) technology globally.
1. DRI as a Core Feedstock in Electric Arc Furnaces
DRI Enhances Control Over Steel Quality
One of the primary uses of DRI is as a main charge material in Electric Arc Furnaces (EAFs). Compared to scrap, DRI offers predictable chemical composition and minimal contamination from tramp elements such as copper or tin. This results in a higher-quality melt—ideal for producing premium grades of steel.
Many of our clients transitioned to DRI in their EAFs after facing inconsistent results with scrap. In one case, a mill producing flat-rolled steel for the automotive sector reported a 15% improvement in surface quality after incorporating 40% DRI into their charge mix.
Productivity and Energy Efficiency Gains
DRI’s uniformity improves furnace efficiency, reduces electrode wear, and lowers power consumption. The result? Increased tap-to-tap speed and lower operational costs. Facilities using hot DRI (HDRI) can take this a step further.
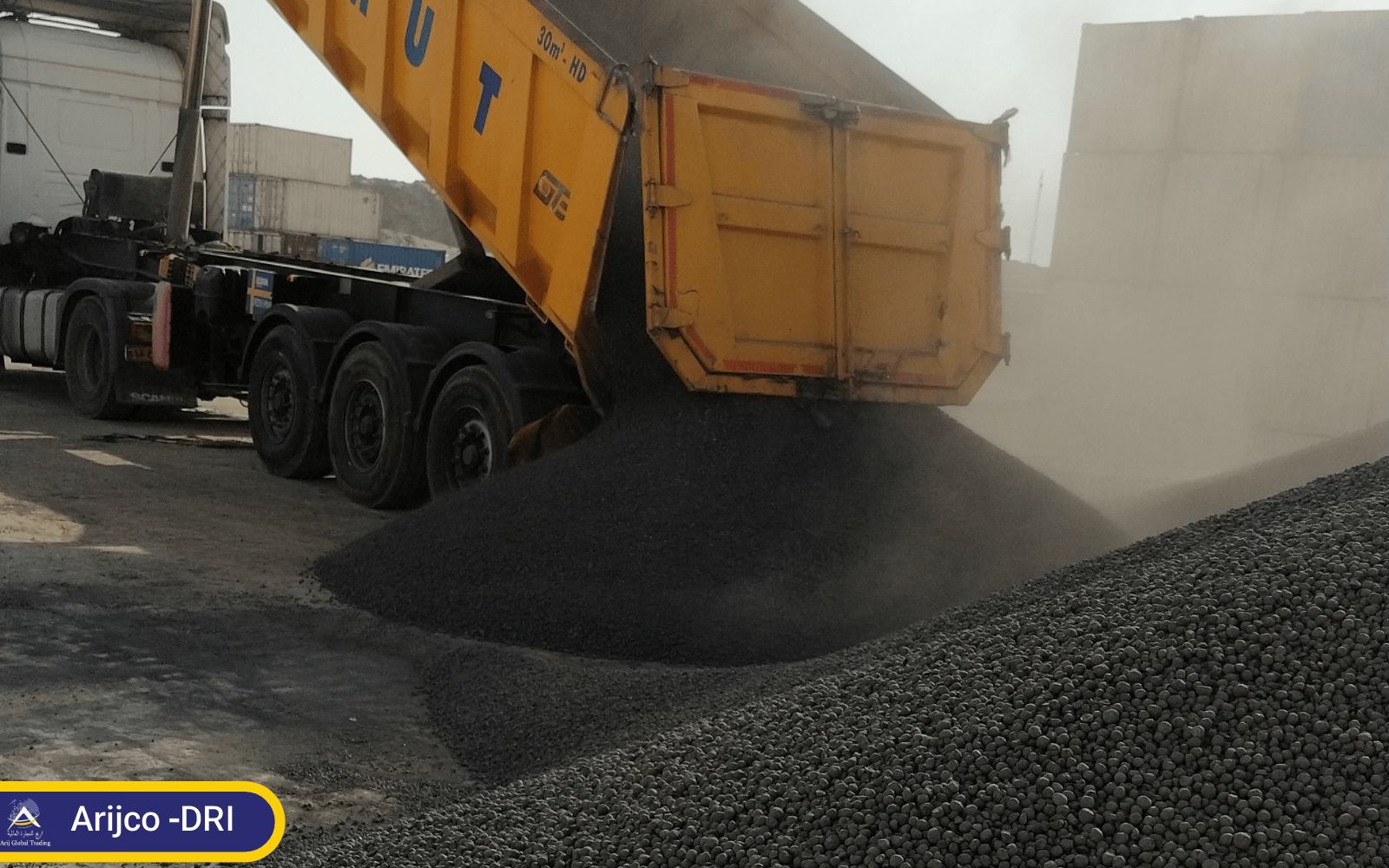
2. Using DRI to Supplement Scrap Metal
Diluting Tramp Elements in Scrap Charges
Scrap remains a valuable resource, but its composition can be highly variable. DRI helps resolve this. When used as a diluent, DRI reduces the concentration of undesirable elements, enabling mills to hit tighter quality specs. This is especially relevant for high-end steel applications such as pipe, structural steel, and specialty alloys.
3. Supporting Hydrogen-Based and Low-Carbon Steelmaking
Future-Ready Steel Production
DRI is central to the future of low-emission steel production. Unlike blast furnaces that depend on coke, DRI processes can be adapted to use green hydrogen as a reducing agent, dramatically reducing carbon emissions.
This makes DRI the ideal raw material for:
- Green steel initiatives.
- Net-zero transition plans.
- Eco-conscious customers requiring EPD-compliant products.
Being an experienced DRI exporter, we’ve already started supporting projects in Europe that align with the 2030 climate agenda by supplying high-grade iron suited for hydrogen DRI processes.
4. Streamlining Steel Plant Logistics and Storage
Simplified Supply Chains
DRI offers notable advantages in transportation and storage. It’s cleaner and less hazardous than scrap, and when sourced from a reputable DRI trader, you get a consistent product specification that reduces delays at the furnace.
From a logistical standpoint, DRI:
- Has predictable moisture content.
- Is stackable and space-efficient.
- Requires minimal pre-treatment.
We advise our clients to store DRI in covered, moisture-controlled facilities to maintain its reactivity and prevent oxidation.
5. DRI in Continuous Casting and Rolling Operations
Integrated Facility Benefits
Using DRI in integrated casting and rolling lines results in consistent input chemistry, which improves:
- Yield during rolling.
- Quality in downstream products.
- Predictability in alloy performance.
We’ve worked with mills in Southeast Asia that upgraded their casting setups after switching to a 60% DRI input, achieving a 7% improvement in end-product uniformity.
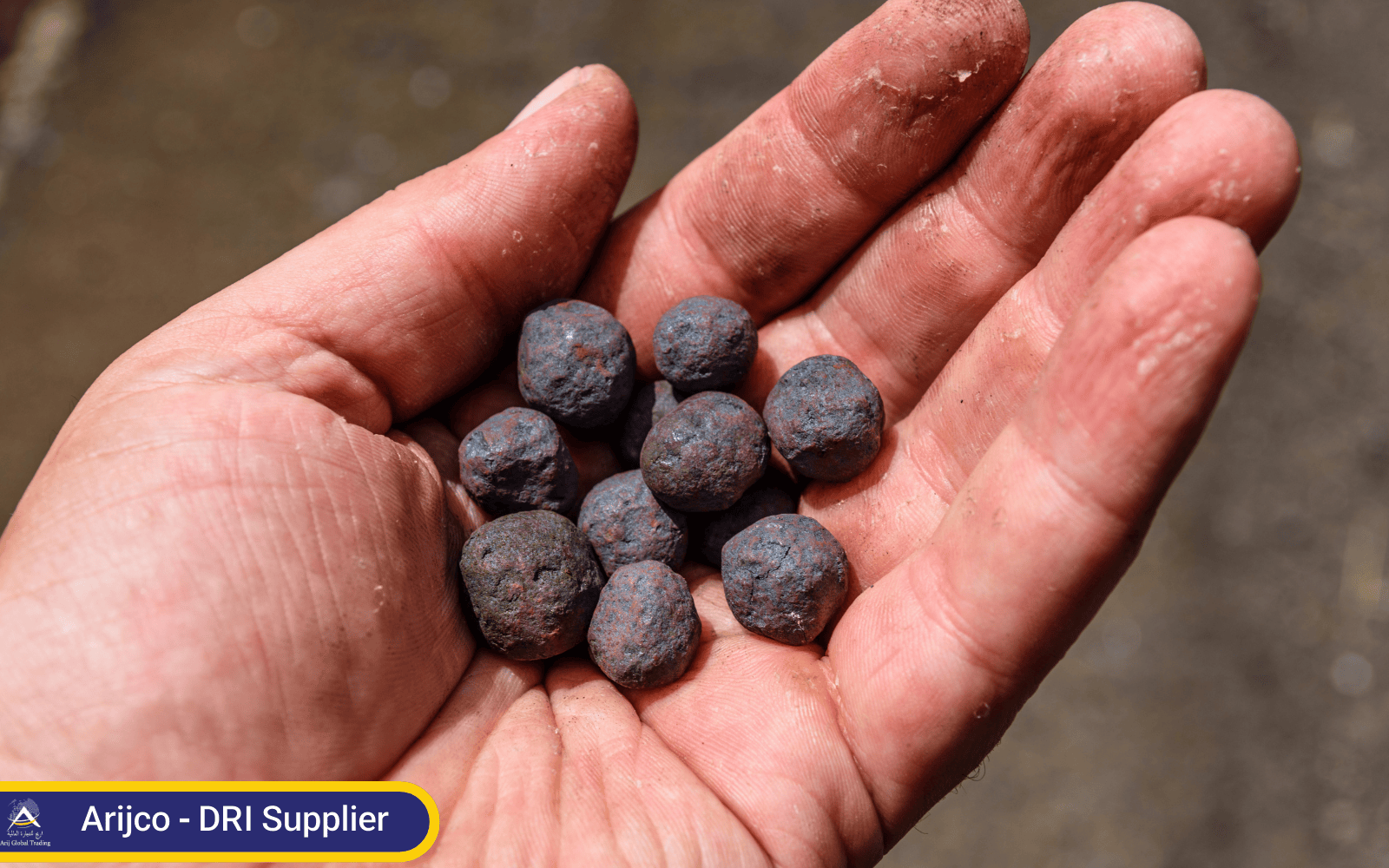
6. Market Outlook and Choosing the Right DRI Supplier
DRI Price Trends and Global Trade
The DRI price is influenced by iron ore quality, energy costs, and shipping logistics. However, its price volatility is often lower than that of scrap, particularly in high-demand regions where scrap availability is tight.
When choosing a DRI supplier, consider:
- Proven export capability as a DRI exporter.
- Flexible packaging and delivery options.
- Support for customized DRI grades (e.g., metallization levels, carbon content).
Conclusion: Strategic Value of DRI for Steel Producers
Modern steel production facilities are rapidly evolving—and DRI is at the center of this transformation. Whether you’re upgrading an EAF operation, exploring hydrogen-based steel, or simply aiming to reduce your reliance on volatile scrap markets, DRI offers clear advantages in quality, efficiency, and long-term cost control.
As a global DRI trader, we’ve helped steelmakers across continents integrate DRI into their operations with tailored supply strategies, technical support, and consistent product delivery. If you’re looking to secure your raw material supply chain while staying competitive in a decarbonizing world, exploring the uses of DRI is no longer optional—it’s essential.