Sponge iron production process discussed herein are selected from known methods of which the references are available and referable. We look at the 4 different methods of producing sponge iron:
- Midrex process
- HYL process (4th generation) or Energiron
- SL / RN process
- Tunnel furnace process
1) Midrex process
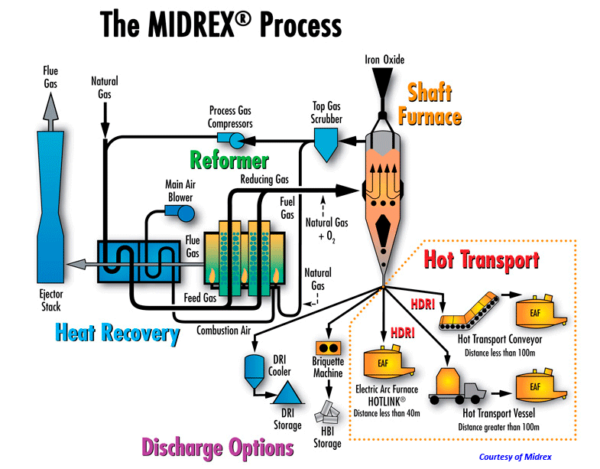
Miderx’s involvement in the direct reduction process can be traced back to the work done by Surface Combustion Company in the 1930s. The company joined Midland Ross in 1959, where the Heat fast processor was under development as a forerunner for the Fastmet process. Surface Combustion was later renamed Midrex.
The first Midrex direct reduction unit, which was installed in Portland State in Oregon, in 1969, had two vertical furnaces with a diameter of 3.7 m and each furnace was designed to produce 150 thousand tons of sponge iron per year. Over the past forty years, Midrex has been designing and building larger units, gradually phasing out Midrex vertical furnaces from inside diameter; It has expanded 3.7 m to 4.25 m and finally to 7.5 m and introduced it to the steel industry.
The main coordinates of the Midrex method are as follows:
- Input iron ore: Input iron ore is in form of cooked pellet in this process and high grade hematite iron ore can be used to a certain extent depending on its condition.
- Reducing agent: Natural gas is broken after the reforming process. In the Midrex process, carbon monoxide gas has a larger share than hydrogen gas in the reducing gas mixture.
- Type of reduction furnace and its conditions: Midrex furnace is a vertical shaft furnace that operates under the pressure slightly less than atmospheric pressure. Its input and output are dynamically sealed and regulated by the input and output flow.
- Reduction temperature: about 850 to 920 °C.
- Process history: since 1969.
- Process position: Fully consolidated and commercialized.
- Process Capacity: The Midrex furnace was initially smaller in diameter and developed towards higher diameter furnaces and greater capacity, as technology improved. The emergence of the generation of mega-modules furnaces with annual capacity of 1.5 million tons or more indicates this. It should be noted, however, that the smaller Midrex process furnaces are still in production circuitry and operate economically. This demonstrates the capability of this process to deliver different capacities.
- Market share: about 60% of the total production of sponge iron
2) HYL process (4th generation) or Energiron

http://nova-gas.blogspot.com/2013/09/144-energiron-direct-reduction.html
The HYL process has undergone quite a number of changes over the past years in terms of its basic design process. The first and second generation of the process is based on direct reduction and using the furnace in conditions varying from the initial stage of reduction to the final stage and discharge. In recent years, the fourth generation of HYL furnaces has entered the market with the aim of removing box reformers.
- Input iron ore: input iron ore is cooked in pellets in this process and the use of hematite iron ore lumps is acceptable, given the rock properties.
- Reducing agent: In this process, as in the Midrex method, the broken natural gas (but with the removal of the reformer) is used as the reducing agent. Also, the use of water vapor is predicted to produce hydrogen reducing gas and increasing it in reduction gas composition. In this process, the amount of hydrogen in the reducing gas mixture is much higher than carbon monoxide, and hydrogen acts as the main reducing agent.
- Type of reduction furnace and its conditions: This furnace is similar to the vertical shaft furnace of the Midrex method. The furnace is sealed by mechanical (hydraulic) mechanisms and atmospheric pressure reaction is much higher and adjusted up to 7 atmospheres to achieve the desired reduction reaction speed.
- Reduction temperature: about 850 to 780 degrees Celsius
- Process history: since 2003.
- Process Position: Unbound but commercialized.
- Capacity: The capacity of the fourth generation furnaces is customizable and highly variable based on the market demand of its technical knowledge. Currently, units of 200 to 800 thousand tons are offered per year.
- Market share: Currently there are 4 modules launched or under construction.
3) SL / RN process
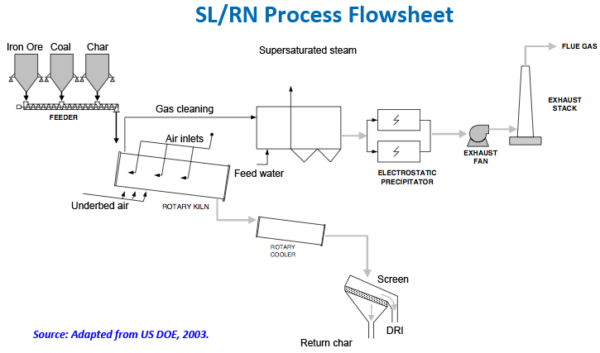
http://downstreamconsulting.com.au/node/11
This process is one of the oldest direct reduction methods and the idea of its structure is based on a horizontal cement kiln. In this method, heat coal (as a reducing agent) is mixed with iron ore and sponge iron is produced in a horizontal furnace.
- Input iron ore: In the Midrex or HYL process, it is generally recommended to use high quality cooked pellets with a maximum of about 30% iron ore lumps. Up to 100% of the lumps can be used in this process and some types of raw pellets will also can be used. The use of magnetite rock in this process is not recommended in this process as it requires high grade hematite iron ore.
- Reducing agent: The advantage of this method is the possibility of using relatively low quality thermal coal as the reducing agent. Coal in the furnace produces carbon monoxide gas, which reduces iron oxide. Despite the relatively high temperature in the furnace, the reaction rate is relatively low and the furnace will be of low capacity. There is no hydrogen gas in this process.
- Type of Reduction Furnace: Rotary Horizontal Furnace that operates at slightly above atmospheric pressure. The main rotary furnace consists of the preheating section and the reduction area, with the gases causes by reaction being discharged at a temperature of about 1000 °C and recycling systems are not anticipated, which is why this energy is generally used to generate electricity. The cooling part of the furnace is a completely separate chamber that is cooled by water from the outside.
- Reduction temperature: about 1000 to 1100 °C.
- Process history: since 1980.
- Process position: Stabilized and commercialized.
- Optimum Capacity: Approximately 100 to 150 thousand tons per module.
- Market share: About 23% of sponge iron total production.
4) Tunnel furnace process
This process is the oldest direct reduction method. In this method, Thermal coal is mixed with iron ore as a reducing agent. Natural gas generates the required reduction temperature, and reduction is performed on Silicon Carbide (SiC) Crucibles in a tunnel furnace.
- Input iron ore: Hematite or magnetite iron ore in form of fine, preferably high grades, such as 65%.
- Reducing agent: The advantage of this method is the possibility of using relatively low quality thermal coal as the reducing agent. Coal in the furnace produces carbon monoxide gas, which reduces iron oxide. The temperature required for reduction is not from coal despite SL / RN, but from the natural gas. Therefore, the pollution in this method is very low.
- Type of reduction furnace: Tunnel furnace consists of three sections: preheating, reduction and cooling areas.
- Reduction temperature: about 1200 to 1250 °C.
- Process history: since 1908 (over 100 years).
- Process position: Stabilized and commercialized.
- Optimum capacity: about 50 thousand tons per module.
- Market share: About 5% of the total production of sponge iron.