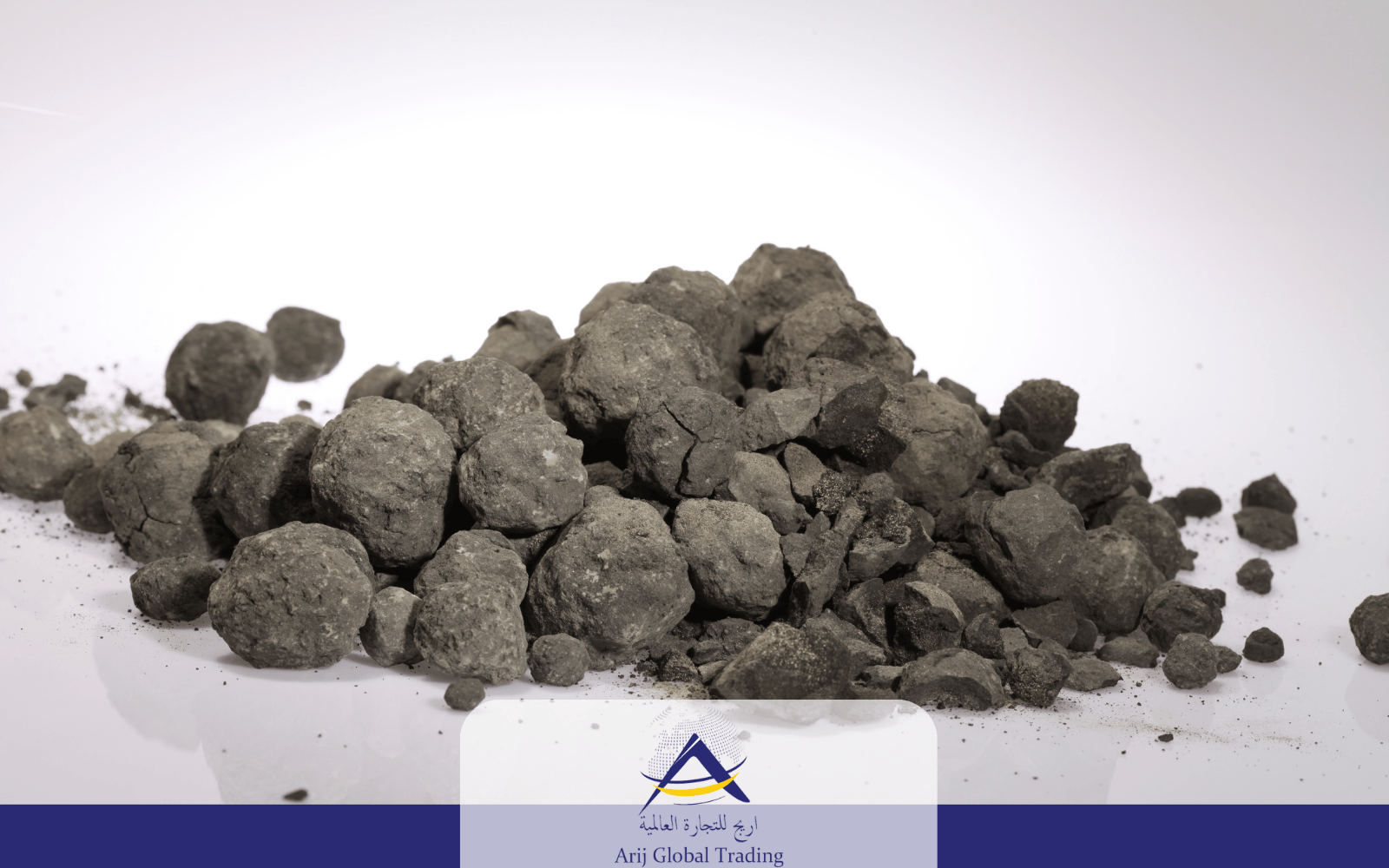
Introduction to Clinker
{Ordinary Portland Cement Clinker} is the essential component in producing Cement, which is made of sintering limestone. In the manufacture of Cement, clinker formed by sintering or fusing without melting to the point of liquefaction, alumina-silicate materials such as clay and limestone during the cement kiln stage and happens as 3 millimeters (0.12 inches) to 25 millimeters (0.98 inches) in diameter.
Clinker History & Traditional manufacturing
In 1825, the Portland cement clinker was first made in a rectified form of the traditional static limekiln. The undeveloped, egg-cup-shaped lime kiln was equipped with a beehive that formed an extension to raise the draft and, therefore, attain the higher temperature needed to make clinker.
For almost half a century, this project and minor adjustments continued as the only method of manufacture.
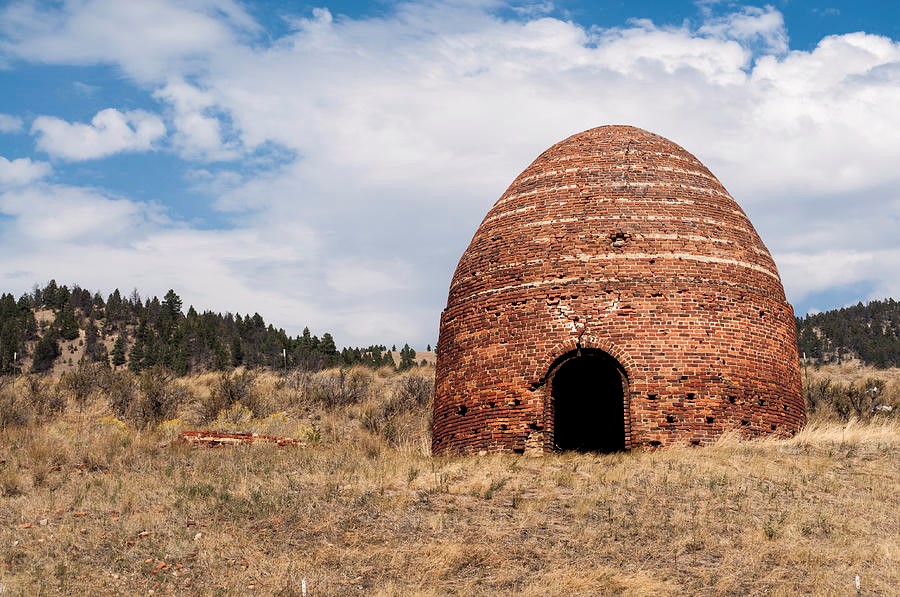
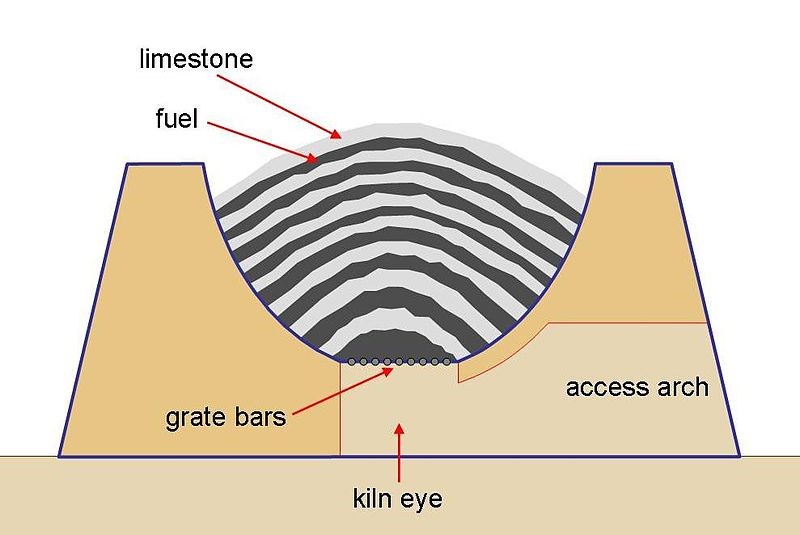
The kiln was surrounded in size by the strength of the lumps of the raw mix: if the charge in the kiln collapsed under its weight, the kiln would be off. For this cause, beehive kilns have not ever finished more than 30 tons of Clinker per batch. A batch took almost seven days to turn around:
- One day to fill the kiln
- Three days to burn off
- Two days to cool
- One day to unload.
Consequently, a kiln would make about 1,500 tons per year at that time.
Clinker: Types, Application & Trade flow
In the cement industry, Clinker is also called “Ordinary Portland Cement Clinker”, “Portland Cement Clinker,” and “Cement Clinker”. Surprisingly, Clinker means a very hard brick in American English and a hard brick used as a paving stone in British English, which is pretty different from the meaning we discuss in the Cement industry. Also, the meaning of Clinker in English is “a mistake or fault, especially a wrong note in music,” which can be mistaken for the Clinker we are discussing here.
Clinker is mostly used to produce cement. Since it can be kept in dry circumstances for several months without noticeable decadence, it has been traded globally in huge amounts. Manufacturers of Cement buy clinker for their cement plants in areas where raw ingredients for cement are rare or inaccessible.
Clinker, joint with some additives and ground into a fine powder, is applied as a binder in cement goods. Diverse elements are added to attain precise properties in the formed cement. Added Gypsum to and ground with Clinker controls the setting time and grants the most significant property of cement: compressive strength. It also avoids the density and coating of the powder at the superficial of the mill and ball wall. Some organic ingredients, such as Triethanolamine (used at 0.1 wt.%), are added as grinding assistance to prevent agglomerated powder. Other additives occasionally used are ethylene glycol, oleic acid, and dodecyl-benzene sulfonate.
Clinker types
The most typical type of Clinker is produced for Ordinary Portland Cement and its combinations. Clinker types vary depending on the cement types for which the Clinker is manufactured. The Portland cement blends aside, some special types of Clinker are mentioned below:
- Sulfate Resistant Clinker
- Low Heat Clinker
- White Clinker
- Low-alkali Clinker
- Belite-Calciumsulfoaluminate-Ternesite (BCT)
You can read the difference between the above types of Clinker later in this article: Types of Clinker.
Cement clinker replacement occurs when Clinker, the main material used in cement manufacturing, is replaced with other cementitious ingredients, such as coal fly ash or blast furnace slag (BFS). These ingredients are the byproducts of other industries and can displace the need to create Clinker.
The top three exporters of Cement clinkers are Spain ($241M), Turkey ($189M) and India ($180M), and its price scales vary from country to country, so a unit price cannot be found anywhere worldwide.
Seminars & Events
Each year, some international Cement seminars and events are held worldwide that you can participate in to enhance your success in this industry. Arab International Cement Conference and Exhibition, for example, is one of those mentioned events, with the below themes:
- Alternative raw materials and related technology
- Alternative Fuels and related technology
- Sustainable Development
- Grinding technology for Clinker and cement
- Burning process
- Filtration and de-dusting
- Solutions for bypassing dust
- Solutions for quarrying wastes and other types of wastes produced in the building material industries
- White Cement
- Introduction to applications in concrete and related materials
- Introduction to applications for brick manufacturing